
COMPRESSED AIR PIPING
A well-planned compressed air piping system is key to efficient airflow in workshops and industrial settings. Getting it right will almost certainly reduce pressure drops, prevent leaks, and improve the efficiency of the air delivery.
From choosing durable compressed air pipework to securing reliable pneumatic pipe fittings, every component affects performance. This guide covers the best materials, fittings, and design tips to optimise your system.
Compressed Air Line Types
We provide a wide range of air compressors to suit every need, including efficient screw compressors, durable piston models, noise-sensitive options, and portable units for flexible use. Available in multiple forms including base mounted, tank mounted, and with or without a dryer.
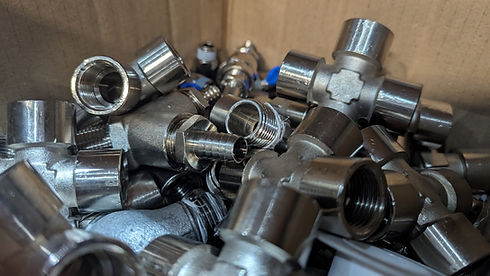
Compressed Air Pipe Fittings
Compressed air pipe fittings and components play a crucial role in maintaining an efficient and leak-free system.
Common fitting types include push-to-connect for quick installation, threaded for secure sealing, compression for tool-free connections, flanged for high-pressure systems, and barbed for flexible hoses.
Essential components such as valves regulate airflow, filters remove moisture and debris, regulators maintain consistent pressure, quick-connect couplings enable fast tool changes, and drain valves help eliminate condensation build-up.
Choosing the right fittings depends on material compatibility, pressure rating, and leak prevention. Modular fittings simplify maintenance and system expansion, while high-quality components improve efficiency, reduce air loss, and lower operating costs.
Compressed Air Line Installation
Proper installation of compressed air piping is essential for efficiency and longevity. Key considerations include:
Pipe Layout: Design a loop or branch system to ensure even air distribution and minimal pressure drops.
Slope & Drainage: Slightly slope pipes and install drain points to prevent moisture build-up.
Support & Expansion: Secure pipes with proper brackets and allow for thermal expansion to avoid stress fractures.
Minimise Leaks: Use high-quality fittings, sealants, and avoid excessive joints.
Avoid Restrictions: Keep bends gradual and use smooth interior pipes to maintain airflow efficiency.
Careful installation reduces pressure loss, extends system lifespan, and lowers energy costs.
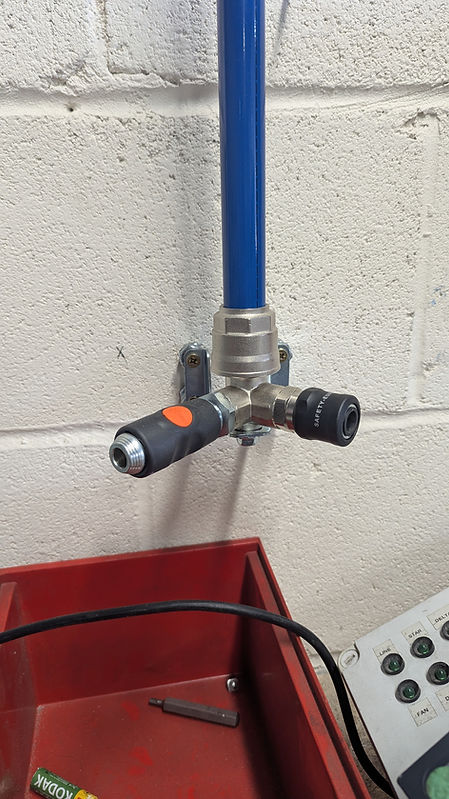
Maintaining Your Compressed Air Line
Regular maintenance and timely upgrades keep your compressed air system running smoothly, cutting down on downtime and energy costs. Check pipes and fittings for leaks or corrosion, as even small leaks can waste a surprising amount of energy. Draining moisture regularly prevents rust and contamination, while cleaning or replacing filters keeps airflow steady and protects your equipment.
Upgrading your pipework can make a big difference in performance and efficiency. Switching to modern materials like aluminium or stainless steel helps reduce pressure drops and improve durability. A better layout or larger diameter pipes can also boost airflow, especially in high-demand setups.
01
Regular Inspections
Check for leaks, corrosion, and loose fittings. Even small leaks can waste energy and reduce system efficiency.
02
Moisture Control
Drain water from tanks and lines frequently to prevent rust, contamination, and damage to tools and machinery.
03
Filter & Component Maintenance
Clean or replace air filters, lubricators, and regulators as needed to maintain consistent airflow and protect equipment from debris.
Frequently asked questions
What is the best material for compressed air pipework?
The best material depends on your needs. Aluminium is lightweight and corrosion-resistant, copper is durable, stainless steel is strong, and plastic options like HDPE are cost-effective.
What size piping do I need for my compressed air system?
Pipe size depends on air demand, pressure, and distance. Larger diameters reduce pressure drops, especially for long runs or high-demand applications.
Can I use PVC pipe for compressed air?
No, PVC is not safe for compressed air as it can become brittle and shatter under pressure. Use materials rated for compressed air systems.
How do I prevent pressure drops in my compressed air piping?
Use smooth, properly sized pipes, minimize sharp bends, avoid long runs, and ensure fittings are airtight to maintain consistent pressure.
How often should I check my compressed air piping for leaks?
Regularly inspect for leaks, at least every few months, as even small leaks can lead to significant energy waste and reduced efficiency.